近年来,精益生产和数字化相关的话题十分火热,一些业内人士提出:“做完精益化提升,再导入数字化的软硬件,才能最大程度地帮助企业”。
但其实,精益管理是数字化转型的基础。只有将精益管理的方法,用数字化的管理手段实现后,才能推动“数据流”形成“价值流”,创造更大的效益。
本期我们来聊聊,数字化如何与精益管理相结合,助力工厂提升生产效率。
大家一定或多或少在日常管理中遇到过这三个“mang”。
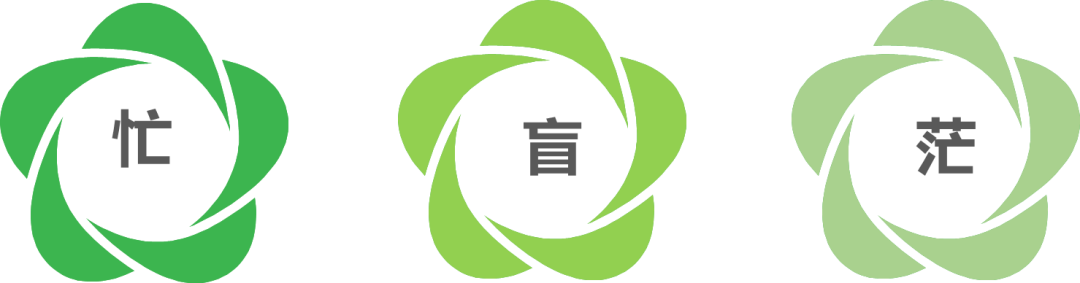
#“忙”:管理人员和生产人员整天都在忙,为啥产量一直上不去?
# “盲”:工厂上下班时间、人员设备都是一样的,为啥产量跟不上人家?
# “茫”:知道工厂效率低,想改善却不知从哪开始,没有思路。
管理与生产的现状已经严重影响许多企业的发展,如何在保证产品质量的前提下持续不断地提升生产效率,让我们从认识工厂效率开始。
效率在生产上,就是我们投入了时间、资金、人员等有形或无形的生产资料,来产出产品或服务的能力。
劳动生产率(UPPH)是用来衡量以人为主的工厂效率及质量的综合指标,在知名制造型企业被广泛使用。
计算公式如下:
将公式进一步拆解,我们将得到提升劳动生产率的几个因素:
# 降低 C/T :生产周期,降低每生产一个产品需要的时间;
#降低损失工时:降低包括设备维修或者等待物料、换模换具的时间;
# 降低员工人数:降低生产员工人数;
#提升良率:提升产品合格率;
#提升总工时
第1招:标准建立,一切以效率提升为核心
第一个准备活动就是基础数据的准备。
我们需要定义一些核心的标准工时、稼动率目标、操作效率、工时平衡率等数据。让一切效率标准可被量化。
Tips:标准工时是如何计算的呢?
标准工时=正常时间+宽放时间
其中,正常时间=平均时间x(1+评比系数)
平均时间:通过历史的生产数据记录、产量的计算以及平时计算的工序时间,得出一个平均时间。
评比系数:比方说员工甲刚开始工作,干的很快,平均时间也短;同时员工乙已经干了5 个小时再进行测量,平均时间就会变长,这时候会考虑乘以一个评比系数。
宽放时间=私事宽放+疲劳宽放+程序宽放+特别宽放+政策宽放+…
私事宽放:根据国际劳工标准协会时间比例,男性乘以5%、女性乘以7%
疲劳宽放:一般乘以4%
稼动率可以简单理解为一台机器设备实际生产数量与可能的生产数量的比值。
计算方式如下:
稼动率=【实际CT*总生产数/负荷时间】*100%
而提升稼动率的目的就是为了提高设备能力的有效利用、彻底消除无效作业的浪费、适应生产方式的变化。
我们通过两种机制的建立进行稼动率的提升:专案改善+突发问题处理。
专案改善的特性是经常发生,且数据量不是很大。这一类的数据可能不起眼,但日积月累以后,会造成很大的浪费。
突发问题的特性是平常每天损耗时间非常小,突然某一天数据变得非常大。
#典型突发问题停机趋势图

我们先进入这样一个生产场景:
工厂某条生产线的第一道工序每小时可以生产 100 个,第二道工序每小时生产 80 个,第三道工序每小时生产 60 个,第四道工序每小时生产 120 个。
这就是一个典型的生产线不平衡,而整个生产线的节拍是由瓶颈工序决定的。
因此,我们要提升线平衡率,就要对生产线的全部工序进行负荷分析,通过调整工序间的负荷分配使各工序达到能力平衡,最终消除各种等待浪费现象,提高生产线的整体效率。

通过以上精益知识的学习,我们发现生产效率的提升很大程度上需要实时、准确的数据支撑。
比如:工厂核心的标准工时、生产良率、各个工位准确的工作时间等等等等。
但现实情况却是,大多数工厂还在依赖工人手写填报、纸质工单收集,这就容易出现纸单污损、丢失,数据手写不易识别的问题。
传统的生产模式,不管是计划的下发,还是数据的反馈,都需要经过多个环节。而每一个环节都像是一个信息漏斗,虽然不是员工刻意造成的,但只要是人力,就难免出现差错。
随着沟通层级的增多,也意味着最终传递到管理层的信息出现偏差的可能性越大,出现错误的数据越多,生产效率的提高又从何谈起?
只有各部门之间实现高效协同,提升生产现场数据的及时性和准确性,才能让数据发挥最大的效用,从而帮助工厂提升生产效率,成为“别人家的工厂”。
1. 「黑湖小工单」—— 打破各部门信息孤岛
通过电子工单下发,生产任务及要求可以实时、点对点的通知到人。相比之前多层级的信息流转,如今「黑湖小工单」实现了信息的扁平化,各个级别都能看到及时准确的生产工单数据,有效避免了信息偏差。
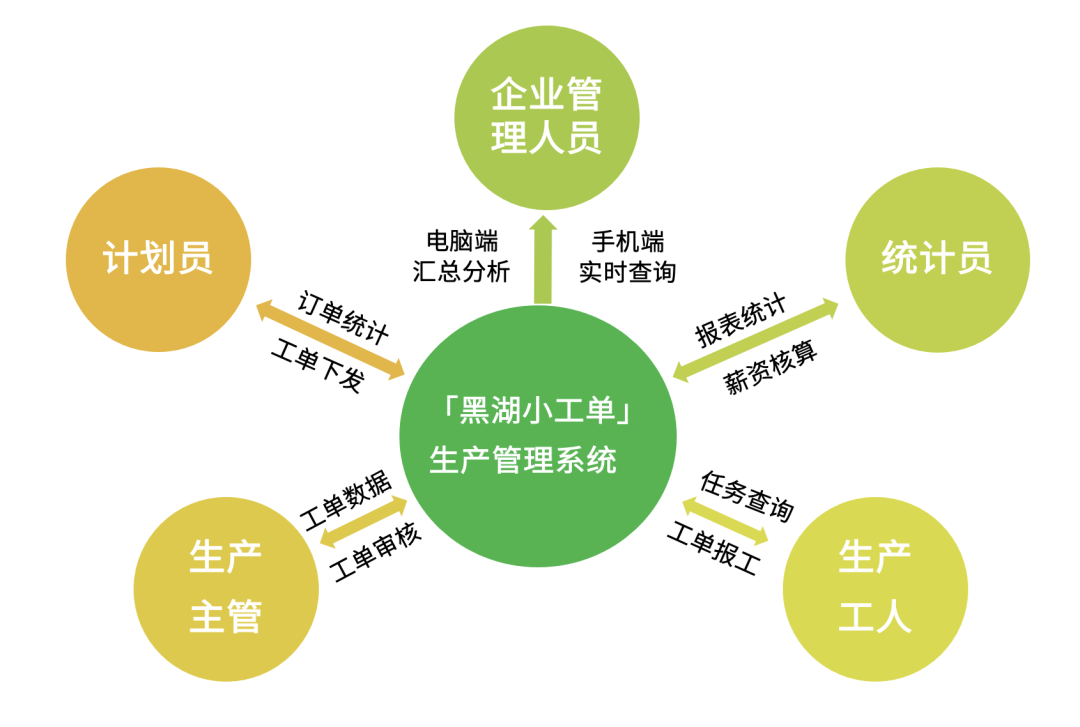
2. 关键效率指标实时统计、实时分析、实时改善
有了前面数据收集的铺垫,管理层可以通过「黑湖小工单」里的工厂全局看板,更直观的了解到车间实时的生产情况,包括生产进度、订单总览、不良品数量、库存数量等等。
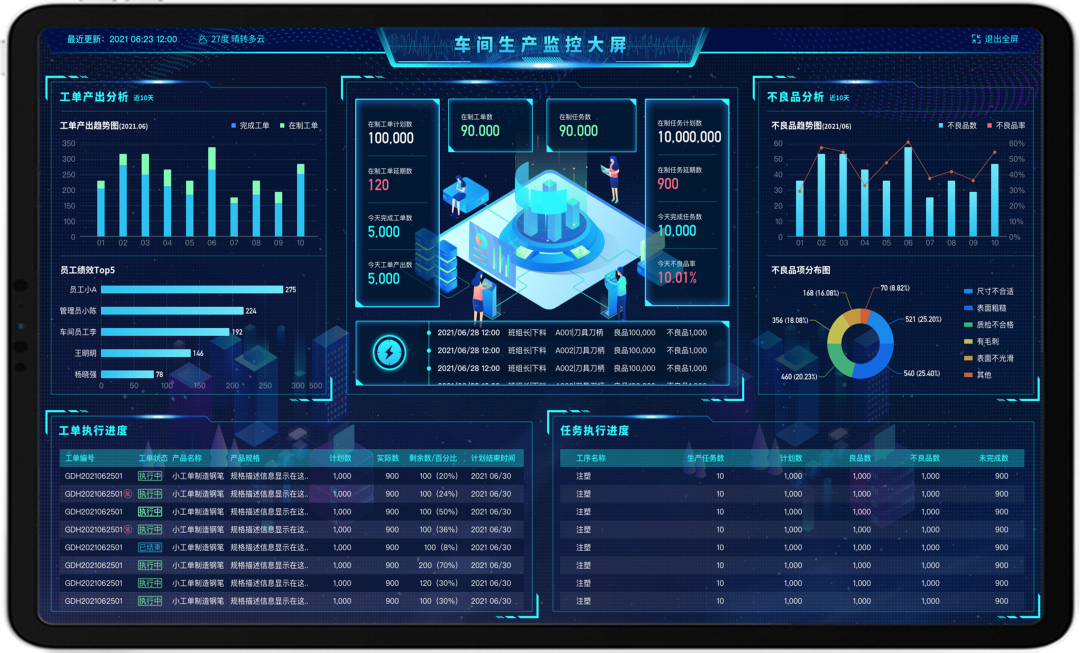
对于管理人员来说,这些准确的数据为后续生产流程优化提供了有力的依据。比如通过计算员工的平均产能、平均生产合格率,可以对低于平均值的员工进行细化的数据分析,是操作技能需要提高,还是生产流程有问题?找到原因后再优化,就可以进一步提高生产效率,真正达到降本增效的目的。
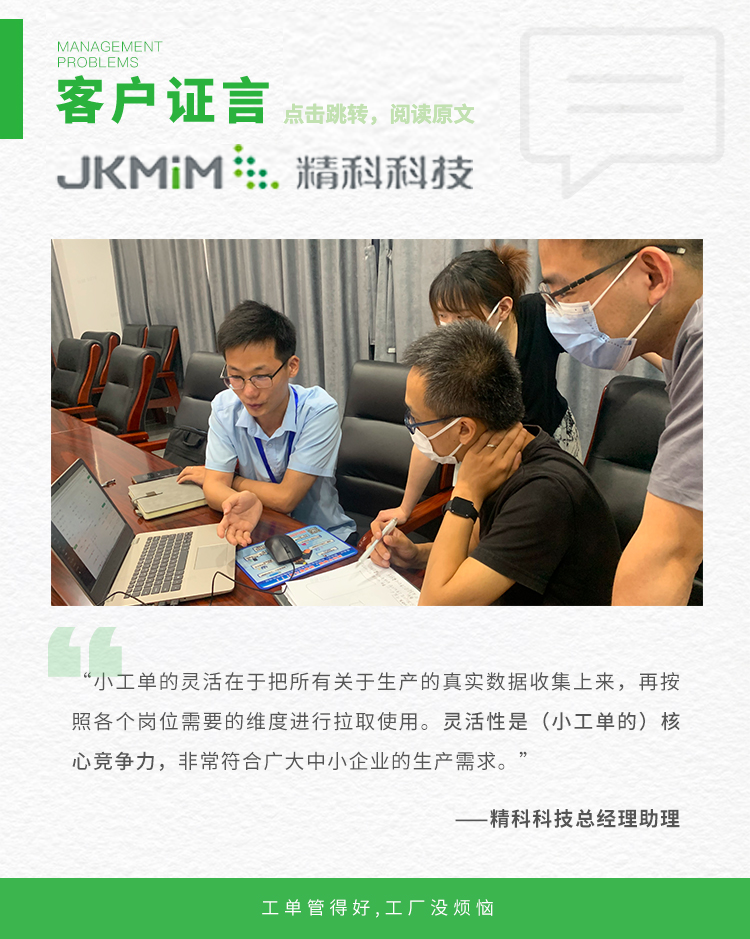
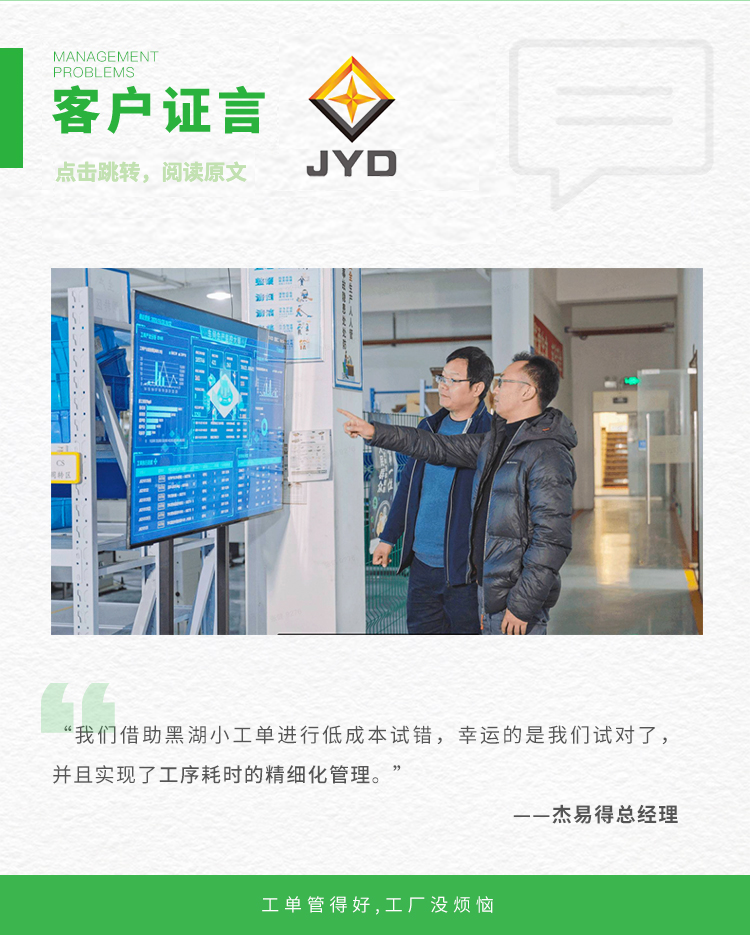